Solid oxide electrolyser cell electrolysers
Overview of the status and impact of the innovation
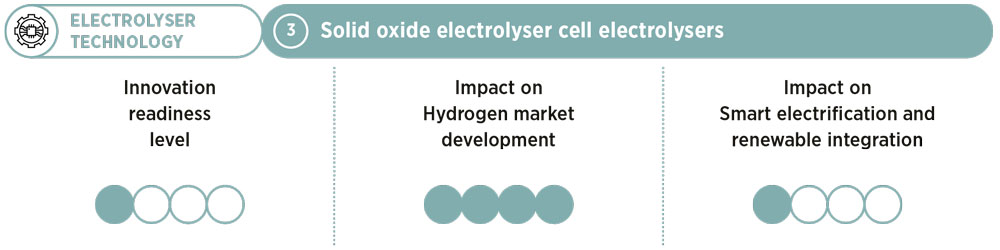
What
SOEC electrolysers operate at very high temperatures (700-850°C) at atmospheric pressure. Using heat energy as well as electricity, they split water into hydrogen and oxygen. The high temperatures increase the overall electrical efficiency of SOEC electrolysers and enable the use of non-precious metals as catalysts. SOEC electrolysers can also electrolyse carbon dioxide (CO2) to carbon monoxide (CO) and oxygen. The CO can then be used to produce syngas, a basic building block for the chemical industry. SOEC electrolysers can also be operated in reverse, producing electricity like fuel cells. This functionality increases their hours of operation and keeps them at operating temperature for longer periods. Most current SOEC electrolysers are small, kilowatt-scale demonstration plants, although some projects have already exceeded 1 MW capacity (Neste, 2021). SOEC electrolysers have high capital costs (at more than USD 2 000/kW for 1 MW stacks), although the target for 2050 is to reduce this to less than USD 200/kW.
Why
Considering that SOEC electrolysers are much less flexible than other electrolyser technologies, they are less suited to direct coupling with variable renewable energy production. However, they do have important advantages. Their use of heat in addition to electricity raises their electrical efficiency. Thus, SOEC electrolysers would bring about a significant reduction in overall electricity demand compared with any other electrolyser technology (IRENA, 2020c). In addition, the heat that they require could be supplied by sources such as industrial waste heat streams or concentrated solar power (CSP) plants. This would facilitate the coupling of SOEC electrolysers to heat production technologies. SOEC electrolysers also enable the production of syngas as well as hydrogen, and the potential for reversable operation increases their lifetimes.
Related kits
Other power innovations
Innovations (30)
-
Technology and infrastructure
- 1 Pressurised alkaline electrolysers
- 2 Polymer electrolyte membrane electrolysers
- 3 Solid oxide electrolyser cell electrolysers
- 4 Anion exchange membrane electrolysers
- 5 Compressed hydrogen storage
- 6 Liquefied hydrogen storage
- 7 Hydrogen-ready equipment
- 8 Digital backbone for green hydrogen production
- 9 Hydrogen leakage detection
-
Market design and regulation
- 10 Additionality principle
- 11 Renewable power purchase agreements for green hydrogen
- 12 Cost-reflective electricity tariffs
- 13 Electrolysers as grid service providers
- 14 Certificates
- 15 Hydrogen purchase agreements
- 16 Carbon contracts for difference
- 17 Regulatory framework for hydrogen network
- 18 Streamline permitting for hydrogen projects
- 19 Quality infrastructure for green hydrogen
- 20 Regulatory sandboxes
-
System planning and operation
-
Business models