High-temperature electricity-based applications for industry
Overview of the status and impact of the innovation
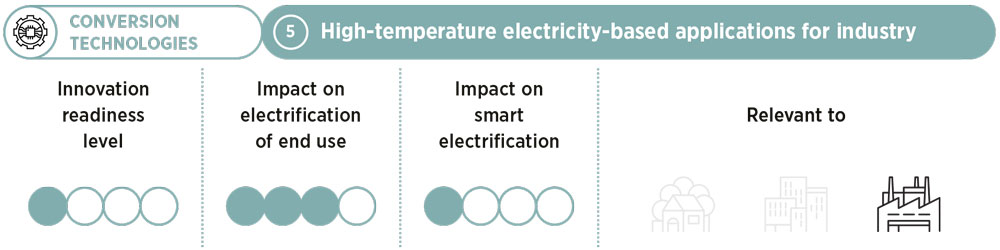
What
Seventy percent of the final energy consumed by European industry in 2015 came from burning fuels, primarily to supply heat (Madeddu et al., 2020). One alternative is to use electricity directly by switching to electric furnaces, electric boilers or other electrolytic processes. Promising solutions are already being developed for the three most difficult-to-decarbonise sectors: chemicals, cement and steel. For the chemical industry, electric crackers (e-crackers) are in the pilot phase. For the cement industry, kilns heated by plasma generators are in the proof-of-concept stage. Meanwhile, the steel industry is piloting electrolytic reduction processes. Finally, as discussed later in this report, these industries could also be electrified indirectly using renewably produced fuels. See Box 5.1 for an overview of power-to-heat technologies, temperature ranges and sectors they can cover.
Why
Replacing fossil fuels with electricity in industry significantly reduces CO₂ emissions when this electricity is produced from renewables. The benefits would be substantial, since industry now consumes about 38% of the total energy used worldwide. While full electrification is challenging, the adoption of mature and ready-to-use solutions (such as low-temperature heat pumps) can significantly increase industry’s electrification rate outside of the difficult-to-decarbonise sectors.
BOX 6.3 E-cracking furnace experimental unit
Shell and Dow have installed an electricity-powered experimental heat steam cracker furnace unit at the Energy Transition Campus in Amsterdam (the Netherlands). This is a key milestone in the effort to decarbonise one of the most carbon-intensive processes of petrochemical manufacturing. The solution could be scaled up by 2025 if tests in 2023 show that it can successfully replace today’s gas-fired steam cracker furnaces.
BOX 6.4 Electrification project of the steel industry in Chenzhou, China
As part of efforts to electrify the Chinese steel industry, a Chenzhou-based casting company is planning to add two additional electricity-based production lines to add capacity. The company plans to adopt the electricity-based production lines instead of the traditional gas-based production line to reduce carbon dioxide emissions.
The project plans to build six energy-saving medium-frequency furnaces and eight resistance furnaces with a total power of 31.2 MW. The annual steel output will increase from 30 000 to 50 000 tonnes, with the annual steel output value increasing to about USD 43 million (CNY 300 million). The annual profit is expected to be approximately USD 10 million (CNY 70 million), with 60 GWh of newly increased electricity consumption. Also, 390 000 tonnes of carbon dioxide and 1 110 tonnes of nitrogen oxide emissions are supposed to be reduced annually.
Thermal storage
TES makes it possible to decouple heating or cooling demand from power generation. Such decoupling offers many important benefits, including greater efficiency, flexibility, security and reliability in energy supply, while also reducing costs and greenhouse gas emissions. As described in this section, thermal energy can be stored at low or high temperatures, 11 or at short or long time scales using the alternatives shown in Figure 6.5 (IRENA, 2020b).
FIGURE 6.5 Operating temperature ranges and time scales for TES technologies
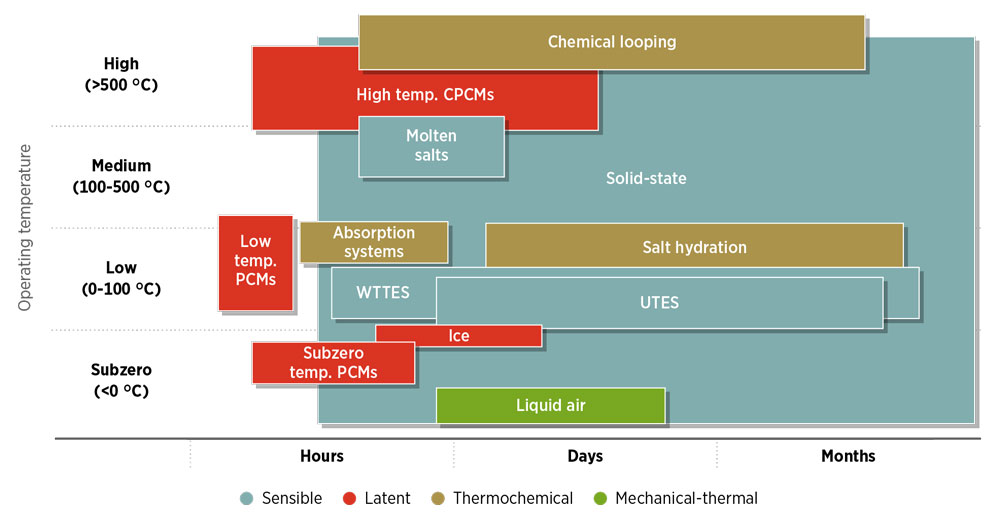
Notes: CPCM = composite phase-change material; PCM = phase-change material; TES = thermal energy storage; UTES = underground thermal energy storage; WTTES = water tank thermal energy storage.
Related kits
Power to heat and cooling innovations
Innovations (35)
-
Technology and infrastructure
- 1 Low-temperature heat pumps
- 2 Hybrid heat pumps
- 3 High-temperature heat pumps
- 4 Waste heat-to-power technologies
- 5 High-temperature electricity-based applications for industry
- 6 Low-temperature thermal energy storage
- 7 Medium- and high-temperature thermal energy storage
- 8 Fourth-generation DHC systems
- 9 Fifth-generation DHC systems
- 10 Internet of Things for smart electrification
- 11 Artificial intelligence for forecasting heating and cooling demands
- 12 Blockchain for enabling transactions
- 13 Digitalisation as a flexibility enabler
-
Market design and regulation
- 14 Dynamic tariffs
- 15 Flexible power purchase agreement
- 16 Flexible power purchase agreement
- 17 Standards and certification for improved predictability of heat pump operation
- 18 Energy efficiency programmes for buildings and industry
- 19 Building codes for power-to-heat solutions
- 20 Streamlining permitting procedures for thermal infrastructure
-
System planning and operation
-
Business models
- 28 Aggregators
- 29 Distributed energy resources for heating and cooling demands
- 30 Heating and cooling as a service
- 31 Waste heat recovery from data centres
- 32 Eco-industrial parks and waste heat recovery from industrial processes
- 33 Circular energy flows in cities – booster heat pumps
- 34 Community-owned district heating and cooling
- 35 Community-owned power-to-heat assets